- Messages
- 11,642
- Location
- Constantine, MI
I am working on a design for a coffee table for a client. He wants the inlays shown in the picture. I can handle the squares, simple template and the right guide bushings, but the curved part has me a bit stumped. I can use a router and trammel to make the grove, but how to fill it?
He wants the inlay to be 1/4" wide, so the stuff you buy for string inlay is too small. He'd like it to be maple, but I may be able to push him towards another species (holly?) if the maple won't work. I thought about laying it in thinner strips and building to the 1/4". Oh, and yes, at 40" diameter it's too big to send to Leo.
Any suggestions?
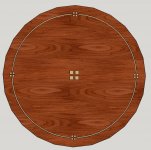
He wants the inlay to be 1/4" wide, so the stuff you buy for string inlay is too small. He'd like it to be maple, but I may be able to push him towards another species (holly?) if the maple won't work. I thought about laying it in thinner strips and building to the 1/4". Oh, and yes, at 40" diameter it's too big to send to Leo.

Any suggestions?
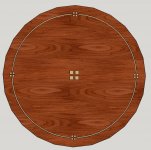