Marty Walsh
Member
- Messages
- 1,396
- Location
- Southern Georgia
Well, I was able to get in a good twelve hours of work on the shed today. Actually, about eleven hours of work, and an hour trying to fight the wind as it tried to wrench sheets of T1-11 from my grip, and retrieving parts and tools that the wind decided to send flying...
I was able to finish the two knee walls on the shop side of the shed. I also got the two last (almost) full sheets installed on the rake walls. I then applied Z-molding to the top of the sheets on the rake wall, and then cut and installed the angled top slivers of sheets.
With the exception of the partial sheet I need to cut in the morning to cover the door opening, the shed is now completely sheathed:
.
.
. 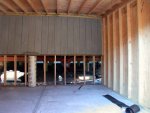
(I just noticed that I need to clean the lens on my camera. Sorry about that...
)
Once I was done outside, I went back inside and finished installing the switch and outlet covers that I painted. Well, those that I was happy with anyway...
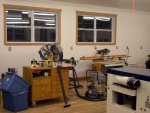
Quite a few needed a second coat:
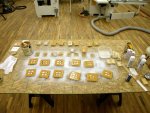
Tomorrow I'll put up that last sheet of T1-11 on the front of the shed. Then cut the two sheets to define the opening.
Then I move on to insulating and sheathing the interior walls that will be part of the 'plenum room'. Then I have to build two walls...one to attach to the shop to define the 'back' of the plenum room, and one to be the actual partition wall that defines the right side of that room.
If I have time and energy left, I'll go get four more bundles of shingles and get those installed so the roof will be complete.
We'll see how far I get tomorrow...
Thanks for following...
- Marty -

I was able to finish the two knee walls on the shop side of the shed. I also got the two last (almost) full sheets installed on the rake walls. I then applied Z-molding to the top of the sheets on the rake wall, and then cut and installed the angled top slivers of sheets.
With the exception of the partial sheet I need to cut in the morning to cover the door opening, the shed is now completely sheathed:
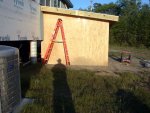
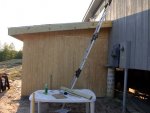
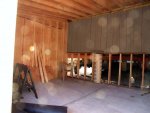
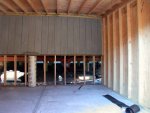
(I just noticed that I need to clean the lens on my camera. Sorry about that...

Once I was done outside, I went back inside and finished installing the switch and outlet covers that I painted. Well, those that I was happy with anyway...

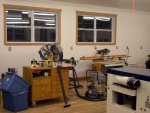
Quite a few needed a second coat:
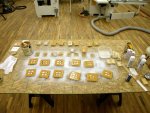
Tomorrow I'll put up that last sheet of T1-11 on the front of the shed. Then cut the two sheets to define the opening.
Then I move on to insulating and sheathing the interior walls that will be part of the 'plenum room'. Then I have to build two walls...one to attach to the shop to define the 'back' of the plenum room, and one to be the actual partition wall that defines the right side of that room.
If I have time and energy left, I'll go get four more bundles of shingles and get those installed so the roof will be complete.
We'll see how far I get tomorrow...
Thanks for following...
- Marty -