- Messages
- 37,098
- Location
- ABQ NM
Since "serial" posts seem to go over well here, I figured I'd start one here to chronicle one of my bowls. Since I wrote this all up for my website, forgive the fact that I'm describing some turning terms and tools in a pretty elementary manner. Some of my family and friends reading my websites are not up to speed on turning terms. (Then again, not all FW members might know what some of the terms mean either.) 
A while back, the Facilities Manager at my office had some long-overgrown shrubbery up-rooted and removed. Being a woodturner, I simply had to see what might be inside some of the bigger pieces of this soon-to-be mulch, so I got permission to take home as much of it as I wanted. Here's a nighttime shot of the truckload I brought home. I cut the wood up after dark at the office...it made it more exciting being able to see the sparks from the chain saw hitting dirt and rocks.
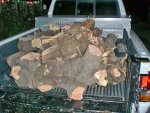
Although my first inclination was that this was some type of Dunno wood, I later determined that it was likely Myoporum, an ornamental, yet invasive exotic shrub from New Zealand. Science lesson over, it was time to try some of this wood out. After several months of procrastination, I finally got one of the root balls cleaned up and ready to try turning. (Thank goodness for pressure washers.) Sorry for the snapshot nature of these pictures.
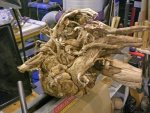
When I "harvested" the wood, I painted the freshly-cut ends to seal them in hopes of preventing cracks from drying. That explains the white part in this shot...
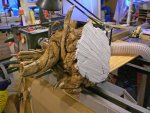
Since that hunk of wood obviously wasn't going to spin real well on my lathe, I did a little chainsaw refinement to get it to a bit more manageable size.
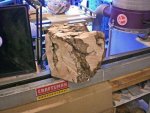
And the white side, with the lathe faceplate attached. (You can see the Hoover Suck-O-Matic dust collector in the background. Click here to see that story.)
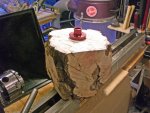
For those of you unfamiliar with woodturning, the red faceplate allows the hunk of wood to be attached to the spindle of the lathe. It looks something like this once it's attached. For those of you who are familiar with turning, you'll note that I don't really have anything solid to turn down to a tenon on side the opposite the faceplate. This will be strictly a faceplate bowl...no chuck. I'll turn off the foot where the faceplate is later.
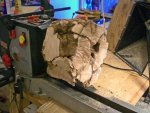
It's quite a blur when it's spinning at 400 or so RPM...
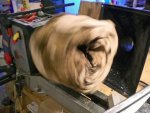
About 20 minutes of beating later, it was round-shaped and looking like this...
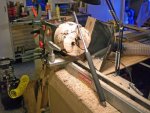
That long black and silver tool is from Monster Tools, and they call it the Monster Indexer with Handle. I call it the Beatin' Stick. It's a very versatile tool, and by far the beefiest "chisel" I have for this type of work. It accepts a range of steel cutting bits. For roughing out this hunk of wood, I attached a 3/8" bit that originally came with my hollowing tools (also from Monster Tools).
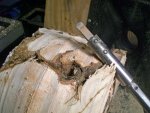
Continued...
A while back, the Facilities Manager at my office had some long-overgrown shrubbery up-rooted and removed. Being a woodturner, I simply had to see what might be inside some of the bigger pieces of this soon-to-be mulch, so I got permission to take home as much of it as I wanted. Here's a nighttime shot of the truckload I brought home. I cut the wood up after dark at the office...it made it more exciting being able to see the sparks from the chain saw hitting dirt and rocks.
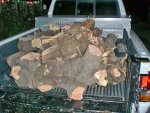
Although my first inclination was that this was some type of Dunno wood, I later determined that it was likely Myoporum, an ornamental, yet invasive exotic shrub from New Zealand. Science lesson over, it was time to try some of this wood out. After several months of procrastination, I finally got one of the root balls cleaned up and ready to try turning. (Thank goodness for pressure washers.) Sorry for the snapshot nature of these pictures.
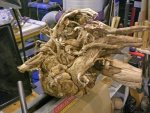
When I "harvested" the wood, I painted the freshly-cut ends to seal them in hopes of preventing cracks from drying. That explains the white part in this shot...
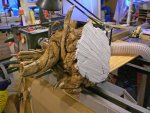
Since that hunk of wood obviously wasn't going to spin real well on my lathe, I did a little chainsaw refinement to get it to a bit more manageable size.
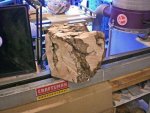
And the white side, with the lathe faceplate attached. (You can see the Hoover Suck-O-Matic dust collector in the background. Click here to see that story.)
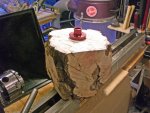
For those of you unfamiliar with woodturning, the red faceplate allows the hunk of wood to be attached to the spindle of the lathe. It looks something like this once it's attached. For those of you who are familiar with turning, you'll note that I don't really have anything solid to turn down to a tenon on side the opposite the faceplate. This will be strictly a faceplate bowl...no chuck. I'll turn off the foot where the faceplate is later.
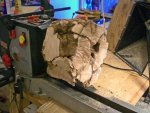
It's quite a blur when it's spinning at 400 or so RPM...
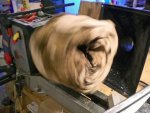
About 20 minutes of beating later, it was round-shaped and looking like this...
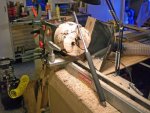
That long black and silver tool is from Monster Tools, and they call it the Monster Indexer with Handle. I call it the Beatin' Stick. It's a very versatile tool, and by far the beefiest "chisel" I have for this type of work. It accepts a range of steel cutting bits. For roughing out this hunk of wood, I attached a 3/8" bit that originally came with my hollowing tools (also from Monster Tools).
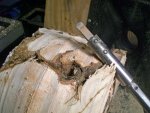
Continued...