Frank Pellow
Member
- Messages
- 2,332
- Location
- Toronto, Ontario, CANADA
(part 1 of 3)
I built my wife Margaret a display case for her birthday on January 1st. I used plans from the book “Display Cases You Can Build” by Danny Proulx (ISBN: 1-55870-606-2) and followed them quite closely. The main difference was that I used dowels in places where Danny advocated biscuits and in others where he advocated mortise and tenon joins. Another difference is that I used 10mm glass for the shelves and 5mm glass in the doors where he suggested 6mm for shelves and 3mm for doors.
Here are some notes extracted from my weekly journal:
2007 Dec 30:
Christmas has come and gone and now I am rushing to get the core part of Margaret’s main birthday present finished. As usual, I left things to the last minute and, this time, the last minute was too late.
On Saturday, after our return from London, I started work on the carcass of the oak display cabinet. The carcass is completely made of sheet goods. In the picture below, the back (made of nominal ½ inch red oak veneer) is being trimmed to size using a guided circular saw:
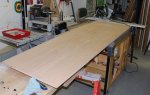
Here, shelf support holes are being drilled into a side (made of nominal ¾ inch red oak plywood) using a home-made template:
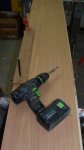
And next dados and rabbets are being routed into the sides using a guided router:
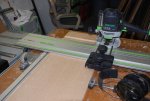
2008 Jan 6:
I actually finished construction of the carcass Tuesday morning (just in time). Here are a couple of pictures, the first showing the glue up with 18 clamps of the back and the second showing what I ended up presenting to Margaret:
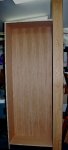
Well, actually I first presented this picture:
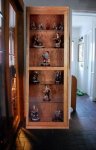
simulating the finished cabinet in our hall, then I took her to the shop and showed her the real thing as so far as it has been built.
I built my wife Margaret a display case for her birthday on January 1st. I used plans from the book “Display Cases You Can Build” by Danny Proulx (ISBN: 1-55870-606-2) and followed them quite closely. The main difference was that I used dowels in places where Danny advocated biscuits and in others where he advocated mortise and tenon joins. Another difference is that I used 10mm glass for the shelves and 5mm glass in the doors where he suggested 6mm for shelves and 3mm for doors.
Here are some notes extracted from my weekly journal:
2007 Dec 30:
Christmas has come and gone and now I am rushing to get the core part of Margaret’s main birthday present finished. As usual, I left things to the last minute and, this time, the last minute was too late.
On Saturday, after our return from London, I started work on the carcass of the oak display cabinet. The carcass is completely made of sheet goods. In the picture below, the back (made of nominal ½ inch red oak veneer) is being trimmed to size using a guided circular saw:
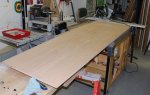
Here, shelf support holes are being drilled into a side (made of nominal ¾ inch red oak plywood) using a home-made template:
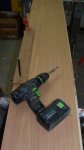
And next dados and rabbets are being routed into the sides using a guided router:
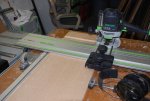
2008 Jan 6:
I actually finished construction of the carcass Tuesday morning (just in time). Here are a couple of pictures, the first showing the glue up with 18 clamps of the back and the second showing what I ended up presenting to Margaret:
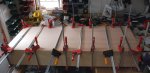
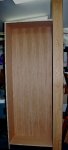
Well, actually I first presented this picture:
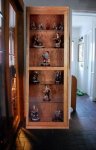
simulating the finished cabinet in our hall, then I took her to the shop and showed her the real thing as so far as it has been built.