I worked with metal and was always fascinated with steel joining systems for large timbers. I read FHB and pored over the details of steel joinery designed by architects. I wondered how, had I been the contractor, I would have solved the hole transfer problems. I knew a lot of architects and builders, so I also knew that the front line builders saved the architects’ you know what regularly. ‘Nuff said.
Finally an opportunity arose for me to play with the data I was gathering for my avocation; home construction. Some friends of mine invited me to help them construct an off the grid, earth sheltered, passive and photovoltaicly powered country retreat.
The roof beam was to be from a great oak they felled on their land. The local sawmill could only handle 16ft. logs, so the beam needed to be spliced in the center. 8” x 12” beams.
Using an old book (still in my bookcase), Simplified Design of Roof Trusses for Architects and Builders, I designed steel splice plates of ½” x 12 steel for green oak wood.
First I drilled the staggered hole pattern in one plate on a Bridgeport vertical mill. Then we clamped the two plates on the beam sections, which were laid out with a chamber.
Then we clamped this jig to the assembly and drilled a 3/8” dia. hole with a 12” bit through the oak and made a mark on the non-drilled plate.
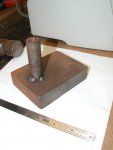
I took the marked plate to my workplace and drilled it on the mill. Just for the heck of it, I dialed in each true position and noted how close the marks were.
The furthest any hole was from true was within a 1/32” circle. Rocket science? No. Good weekend accomplishment? I thought so.
My friends snugged up the bolts regularly as the wood dried, and the house is still standing! I’d have felt really badly had it fallen down.
Frank