- Messages
- 36,618
- Location
- ABQ NM
Here's a jig I use for almost every cutting board I make. It gives me a consistent corner radius using a flush cutting bearing bit on the router table. It's a piece of scrap BB ply with a couple maple stop blocks glued and gunned to the edges. I shaped the radius corner on the jig by eye and by feel with the bandsaw, rasps and sandpaper. Prior to making this jig, I was doing them by eye, so I already had a bit of practice. I added a drawer pull handle to make sure I keep my fingers out of the spinny parts. This jig was also a place for me to practice my shellac-applying skills, which, as the pics prove, are sorely lacking.
With no further ado...
The top side:
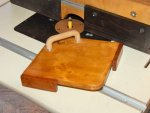
The bottom side:
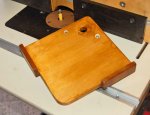
Sitting in place ready for use:
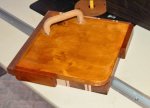
In action:
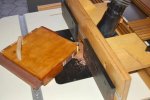
After the cut:
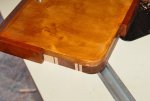
This will be old news to the more experienced folks here, but for the benefit of my fellow newbies, when making cuts like this (transitioning from long grain to end grain) with a router (and I'd guess a shaper, too) you have to pay attention to the grain direction. Always start the cut on the longer grain and end the cut on the end grain. Otherwise, there's a good chance you'll splinter or otherwise mess up the corner. With this jig, I'm feeding the piece from right to left, so I always make sure the long grain is on the left side of the jig. This means I can cut two of the corners, then I have to flip the board over to do the other two corners.
After I radius the corners, I usually put a bullnose edge on the board by making top and bottom passes with a roundover bit, followed by a lot of sanding. I didn't get pics of the board shown in the examples above before it was delivered as part of a set to the customer, but here's the typical end result:
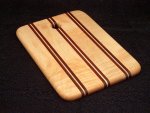
The top side:
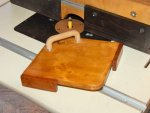
The bottom side:
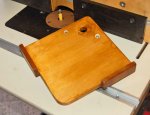
Sitting in place ready for use:
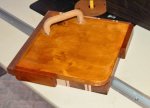
In action:
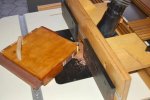
After the cut:
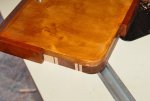
This will be old news to the more experienced folks here, but for the benefit of my fellow newbies, when making cuts like this (transitioning from long grain to end grain) with a router (and I'd guess a shaper, too) you have to pay attention to the grain direction. Always start the cut on the longer grain and end the cut on the end grain. Otherwise, there's a good chance you'll splinter or otherwise mess up the corner. With this jig, I'm feeding the piece from right to left, so I always make sure the long grain is on the left side of the jig. This means I can cut two of the corners, then I have to flip the board over to do the other two corners.
After I radius the corners, I usually put a bullnose edge on the board by making top and bottom passes with a roundover bit, followed by a lot of sanding. I didn't get pics of the board shown in the examples above before it was delivered as part of a set to the customer, but here's the typical end result:
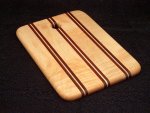