- Messages
- 36,983
- Location
- ABQ NM
As mentioned in an earlier thread, my Sears lathe was showing signs of a slipping belt in the reeves drive. I looked things over and couldn't find anything to adjust to directly to change the belt tension in the reeves drive, so I figured it was the belt. Keep in mind that I was pretty ignorant about how the reeves drive worked. I knew the lower wheel adjusted to change the width of it, but it seemed the upper wheel was fixed in place.
I ordered and received a new belt from Sears (highway robbery...$63 for a little toothed belt that's apparently proprietary to Sears, and I now know, Palmgren). Put the new belt in last night, and it made no difference. I was bummed. Trying to figure out how to talk LOML into letting me buy a new lathe.
While I was in the process of writing up the long sad story to post here with for FW buddies, it dawned on me that the upper wheel (the spring-loaded one) simply had to move in order for the drive to work. (Remember the part where I said I was ignorant?) So at about midnight thirty, I went back out into the shop and figured it out.
I took the belt off, and despite a bit of pushing and pulling, the upper wheel was not adjusting. I could see the shaft had some rust on it, but the two wheel halves were stuck in the 'apart' configuration. I even sprayed a bit of WD-40 on it and reached in and tried to shine things up a bit with steel wool. As it turns out, it's a good thing that my efforts didn't free up the stuck wheel (or sheave, I guess it's called) right then, with my fingers in between the two halves. After a little light tapping with a ball pein hammer, all of a sudden it became unstuck, and WHACK! the sheave slammed into the other half of the wheel. I breathed an audible sigh of relief since my fingers were out of the way by then. (Otherwise, I'd be typing this left-handed today. That thing would have pancaked three fingertips in a heartbeat.) Now it was time to get the wheel off and get things clean and smooth again.
I'd read Darrell Feltmate's web narrative of tearing one of these Sears lathes apart, and he had a great trick for releasing the spring tension on the upper wheel without shooting metal bits across the shop. I'll let the following pics tell the the rest of the story:
Here's a shot showing the 'apart' position the upper wheels were stuck in. (This was actually taken after I fixed everything, but it's to show the relative position of the wheel halves when I started, since I forget to get a pic when I first started.):
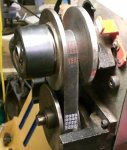
Using a piece of 1/4-20 all-thread and a hunk of scrap steel with a couple holes tapped in it, I made a jig to allow me to put some tension on the spring (to release the snap ring) then de-tension the spring safely. Good thing I did this, since the spring was even stronger than I'd originally imagined. Here's the drive side of the contraption...I've already popped the snap ring off in the pic:
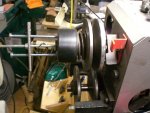
And here's the other end of the all-thread, with just a couple washers and a nut. I slipped a deep socket over this, cranked it by hand and very easily tightened or loosened the spring tension. (Used a pair of vice grips to keep the all-thread from spinning as I turned.)
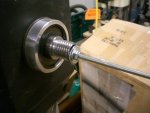
Here's a shot after I've released the tension from the spring:
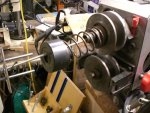
Here's a pic showing how the pully shaft looked before cleanup. There's a bit of WD-40 on it, but you can see the rust:
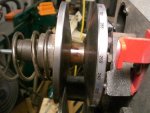
I pulled the outer half of the upper wheel completely off, and after a bit of time with the drill-mounted wire brush, the shaft cleaned up nicely. (I forgot to take the pic until I was in the process of reassembling the whole thing.) I put a bit of dry graphite lube on the shaft, and the sheave moves like it's on ice:
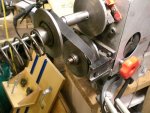
Now it all works as it should. When the lower pulley is set wide (via the red knob), the spring ensures the upper pulley goes narrow. When the lower while is narrow, the upper wheel is now wide. No more slipping!
Slow speed:
Fast speed: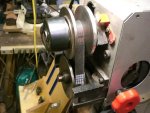
I'm a happy camper (for now)!
I ordered and received a new belt from Sears (highway robbery...$63 for a little toothed belt that's apparently proprietary to Sears, and I now know, Palmgren). Put the new belt in last night, and it made no difference. I was bummed. Trying to figure out how to talk LOML into letting me buy a new lathe.
While I was in the process of writing up the long sad story to post here with for FW buddies, it dawned on me that the upper wheel (the spring-loaded one) simply had to move in order for the drive to work. (Remember the part where I said I was ignorant?) So at about midnight thirty, I went back out into the shop and figured it out.
I took the belt off, and despite a bit of pushing and pulling, the upper wheel was not adjusting. I could see the shaft had some rust on it, but the two wheel halves were stuck in the 'apart' configuration. I even sprayed a bit of WD-40 on it and reached in and tried to shine things up a bit with steel wool. As it turns out, it's a good thing that my efforts didn't free up the stuck wheel (or sheave, I guess it's called) right then, with my fingers in between the two halves. After a little light tapping with a ball pein hammer, all of a sudden it became unstuck, and WHACK! the sheave slammed into the other half of the wheel. I breathed an audible sigh of relief since my fingers were out of the way by then. (Otherwise, I'd be typing this left-handed today. That thing would have pancaked three fingertips in a heartbeat.) Now it was time to get the wheel off and get things clean and smooth again.
I'd read Darrell Feltmate's web narrative of tearing one of these Sears lathes apart, and he had a great trick for releasing the spring tension on the upper wheel without shooting metal bits across the shop. I'll let the following pics tell the the rest of the story:
Here's a shot showing the 'apart' position the upper wheels were stuck in. (This was actually taken after I fixed everything, but it's to show the relative position of the wheel halves when I started, since I forget to get a pic when I first started.):
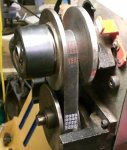
Using a piece of 1/4-20 all-thread and a hunk of scrap steel with a couple holes tapped in it, I made a jig to allow me to put some tension on the spring (to release the snap ring) then de-tension the spring safely. Good thing I did this, since the spring was even stronger than I'd originally imagined. Here's the drive side of the contraption...I've already popped the snap ring off in the pic:
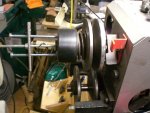
And here's the other end of the all-thread, with just a couple washers and a nut. I slipped a deep socket over this, cranked it by hand and very easily tightened or loosened the spring tension. (Used a pair of vice grips to keep the all-thread from spinning as I turned.)
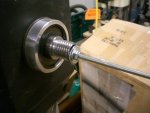
Here's a shot after I've released the tension from the spring:
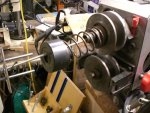
Here's a pic showing how the pully shaft looked before cleanup. There's a bit of WD-40 on it, but you can see the rust:
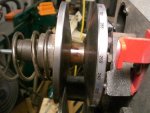
I pulled the outer half of the upper wheel completely off, and after a bit of time with the drill-mounted wire brush, the shaft cleaned up nicely. (I forgot to take the pic until I was in the process of reassembling the whole thing.) I put a bit of dry graphite lube on the shaft, and the sheave moves like it's on ice:
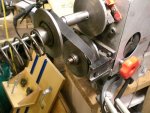
Now it all works as it should. When the lower pulley is set wide (via the red knob), the spring ensures the upper pulley goes narrow. When the lower while is narrow, the upper wheel is now wide. No more slipping!
Slow speed:
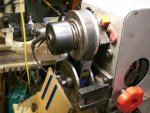
Fast speed:
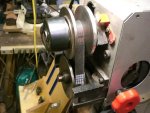
I'm a happy camper (for now)!