Stuart Ablett
Member
- Messages
- 15,917
- Location
- Tokyo Japan
.......OK, not quite "Free" but dirt cheap for sure........
I bought the Beall wood threading tap, sized for my Nova DVR 3000 lathe, that would be 1 1/4" 8 TPI.
I'll show you how it works.......
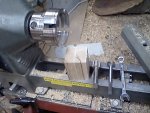
OK here is the basic set up, I have;
A block of wood, (dense hardwood, side grain is the best)
A chuck and jaws that will hold said block of wood
A 14mm box end wrench
A Dill bit sized for the tap you have for your lathe
A wood tap, sized for your lathe
A dill chuck with a MT#2 on it to go into the tail stock
A lathe, and some Pam cooking spray
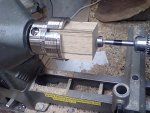
You start by putting the wooden block in the chuck, and the drill chuck in the tailstock and the drill bit, in the drill chuck
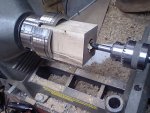
The you drill the hole, with the lathe on a fairly slow speed, I find that about 400 rpm just right.
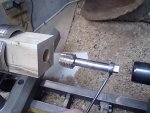
Make sure you clean the hole out well, then you remove the drill chuck and bit from the tail stock, and get the wood tap and the 14mm box end wrench.
I put the box end of the wrench on the square part of the tap, with the wrench on there so the wrench angles towards the headstock, not the tail stock.
From this point on the lathe is used UNPOWERED until the tapping is finished!
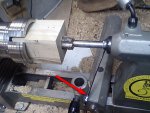
You can see the wrench here contacting the banjo, this holds the wrench from turning, which, is like having a third hand. BTW, Beall does recommends to do things slightly differently, they use the open end, which works, but I find this way, I can concentrate on keeping the tap going into the wood more consistently. (the RED arrow show the wrench contacting the banjo)
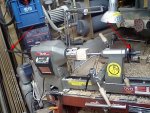
OK, now you move up the tail stock, without anything in the MT hole, the end of the tap goes in there. Move the tail stock so the end of the tap goes in the hole of the MT and the tap goes in the hole you just drilled, with the wrench contacting the banjo, you are now free to turn the spindle of the lathe with one hand and the tail stock with the other hand. You can see the knock out bar I put in the handle on the spindle side, this makes it a lot easier to turn. The tail stock is turned to apply only slight pressure on the tap, once the tap starts to dig in, it pulls itself into the wood.
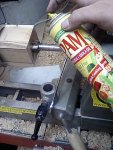
A shot of Pam cooking spray makes this even easier
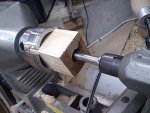
When the tap bottoms out, stop turning, if you keep going, you can split the block of wood.
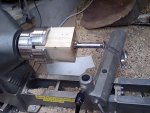
Pull the tailstock out of the way, and lock the spindle on your lathe, then using the wrench, back the tap out of the hole
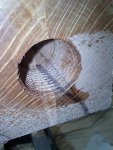
You should have some nice threads in your hole now.........
Cont..........
I bought the Beall wood threading tap, sized for my Nova DVR 3000 lathe, that would be 1 1/4" 8 TPI.
I'll show you how it works.......
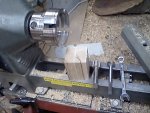
OK here is the basic set up, I have;
A block of wood, (dense hardwood, side grain is the best)
A chuck and jaws that will hold said block of wood
A 14mm box end wrench
A Dill bit sized for the tap you have for your lathe
A wood tap, sized for your lathe
A dill chuck with a MT#2 on it to go into the tail stock
A lathe, and some Pam cooking spray
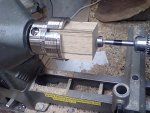
You start by putting the wooden block in the chuck, and the drill chuck in the tailstock and the drill bit, in the drill chuck
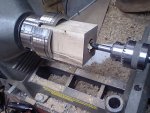
The you drill the hole, with the lathe on a fairly slow speed, I find that about 400 rpm just right.
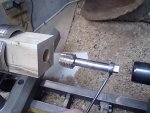
Make sure you clean the hole out well, then you remove the drill chuck and bit from the tail stock, and get the wood tap and the 14mm box end wrench.
I put the box end of the wrench on the square part of the tap, with the wrench on there so the wrench angles towards the headstock, not the tail stock.
From this point on the lathe is used UNPOWERED until the tapping is finished!
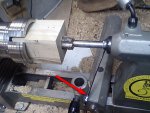
You can see the wrench here contacting the banjo, this holds the wrench from turning, which, is like having a third hand. BTW, Beall does recommends to do things slightly differently, they use the open end, which works, but I find this way, I can concentrate on keeping the tap going into the wood more consistently. (the RED arrow show the wrench contacting the banjo)
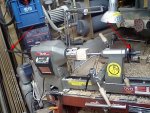
OK, now you move up the tail stock, without anything in the MT hole, the end of the tap goes in there. Move the tail stock so the end of the tap goes in the hole of the MT and the tap goes in the hole you just drilled, with the wrench contacting the banjo, you are now free to turn the spindle of the lathe with one hand and the tail stock with the other hand. You can see the knock out bar I put in the handle on the spindle side, this makes it a lot easier to turn. The tail stock is turned to apply only slight pressure on the tap, once the tap starts to dig in, it pulls itself into the wood.
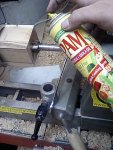
A shot of Pam cooking spray makes this even easier
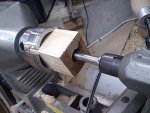
When the tap bottoms out, stop turning, if you keep going, you can split the block of wood.
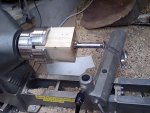
Pull the tailstock out of the way, and lock the spindle on your lathe, then using the wrench, back the tap out of the hole
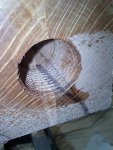
You should have some nice threads in your hole now.........
Cont..........