glenn bradley
Member
- Messages
- 11,640
- Location
- SoCal
There is a near-floor-to-ceiling linen cupboard at the end of a hallway. This is situated so that you see it if you look down the hall when entering the house, walk down the hall to the bathroom or to go to a guestroom . . . in general it is in-your-face. It is not bad per se; it's just that it screams 35 year old contractor grade built-in.
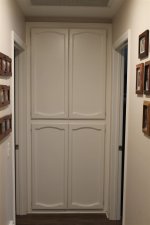
Working with LOML as design consultant "we" are wanting something more like this.
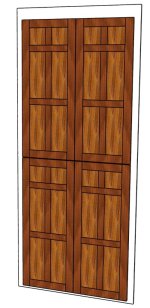
We talked about various materials and styles. I even made a run to the lumber yard. If they would have had some red birch or red alder that was wide enough I would have gone with it. Alas, it was not to be. SWMBO says it shall be sepele. Ever since I built her a buffet out of sepele she has been hooked on the stuff. I pull some stock out of the racks.
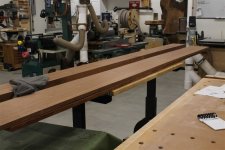
I use my "chop saw" to break down a thick plank that will supply all the floating panels. I like to take pieces from the same board (or boards from a flitch). This makes figure and color matching much easier.
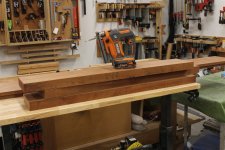
These get the usual face joint, plane faces parallel, edge joint routine.
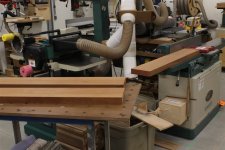
We all have a feel for what material we free hand at the bandsaw and what material we employ some handling aids to process. The board size is right on the line of what I like to muscle through a resawing so I add some feather boards and an outfeed.
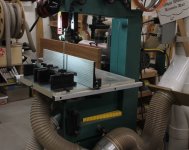
I rip 1/2" off the blanks.
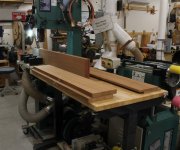
I use the jointed face of the remainder of each blank to re-plane the faces parallel. I then adjust the feather boards and saw another 1/2" off the remainders.
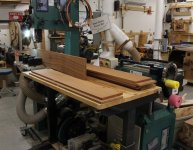
These blanks get set aside to get comfy while I work on some frame stock.
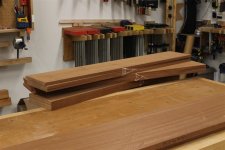
I will mill them to final size in a day or two.
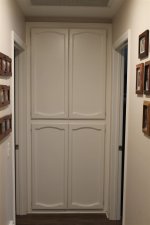
Working with LOML as design consultant "we" are wanting something more like this.
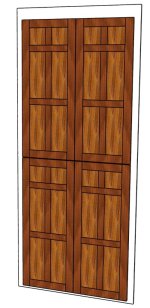
We talked about various materials and styles. I even made a run to the lumber yard. If they would have had some red birch or red alder that was wide enough I would have gone with it. Alas, it was not to be. SWMBO says it shall be sepele. Ever since I built her a buffet out of sepele she has been hooked on the stuff. I pull some stock out of the racks.
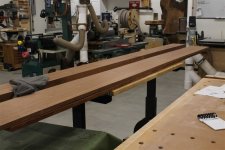
I use my "chop saw" to break down a thick plank that will supply all the floating panels. I like to take pieces from the same board (or boards from a flitch). This makes figure and color matching much easier.
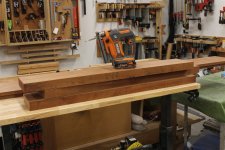
These get the usual face joint, plane faces parallel, edge joint routine.
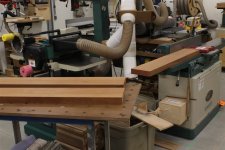
We all have a feel for what material we free hand at the bandsaw and what material we employ some handling aids to process. The board size is right on the line of what I like to muscle through a resawing so I add some feather boards and an outfeed.
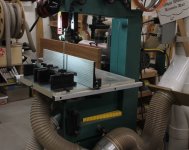
I rip 1/2" off the blanks.
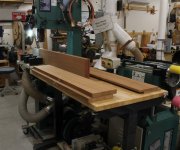
I use the jointed face of the remainder of each blank to re-plane the faces parallel. I then adjust the feather boards and saw another 1/2" off the remainders.
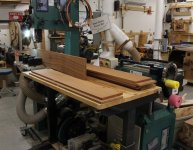
These blanks get set aside to get comfy while I work on some frame stock.
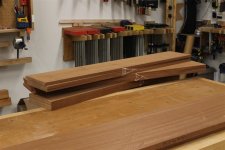
I will mill them to final size in a day or two.