edward alexander
Member
- Messages
- 141
- Location
- smithville,tx.
part five-
the last post showed a test piece out of the steam box and in a mold to find how much spring-back i will have-the mold is a piece of aspin that i drew a curve on and band- sawed -this is the curve i want to use-
when the test piece comes out from the mold it springs back 1/2" -
test piece-
i make a mold from a piece of fir timber compensating for the spring-back-
i make a backing strap from a 1 1/4" bandsaw blade-i cut two 36" lengths grind off the teeth and use duct (duck) tape to hold the two together-
also i cut two pieces of 1/16" plastic to put on each side of the piece of walnut i'll be bending-this is so i want get weird colors from the metal strap and from the fir-
i make a simple drying jig-
then it's for real-#1- i need nine-
i steam three at a time one hour plus-then in the mold for 15 min. then in the drying jig for 24 hours-
the real thing-
it all revolves around this curve-now that i have it for real i can make a true templet for the legs and a mold for the curved veneer panels-
templet-
to make the mold for the panels i use a piece of fir-
i join two of these pieces and band saw the curve- then i line it with 1/16" plastic-
more to come-
alex
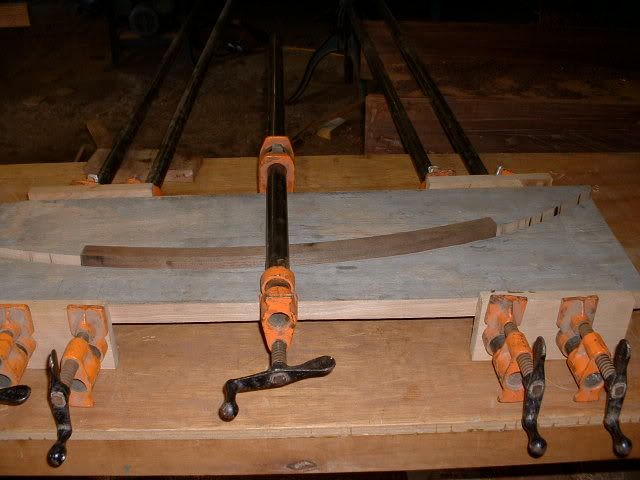
the last post showed a test piece out of the steam box and in a mold to find how much spring-back i will have-the mold is a piece of aspin that i drew a curve on and band- sawed -this is the curve i want to use-
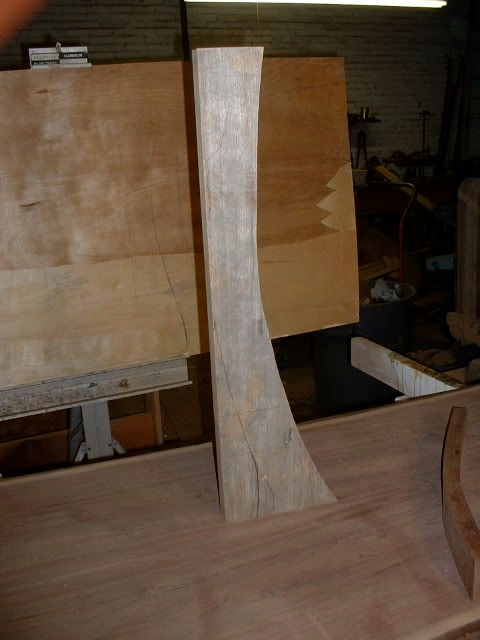
when the test piece comes out from the mold it springs back 1/2" -
test piece-
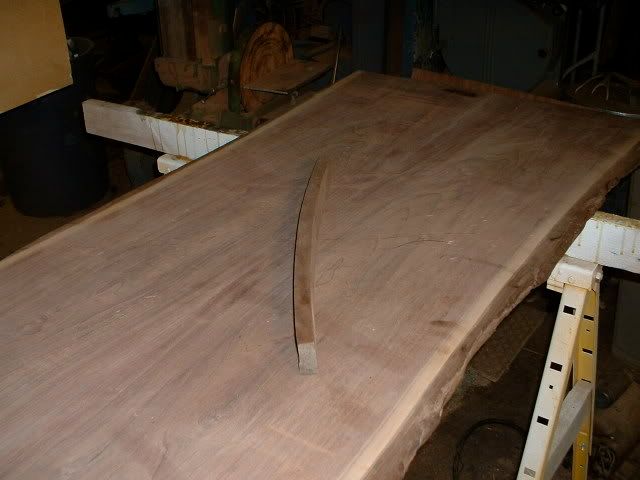
i make a mold from a piece of fir timber compensating for the spring-back-
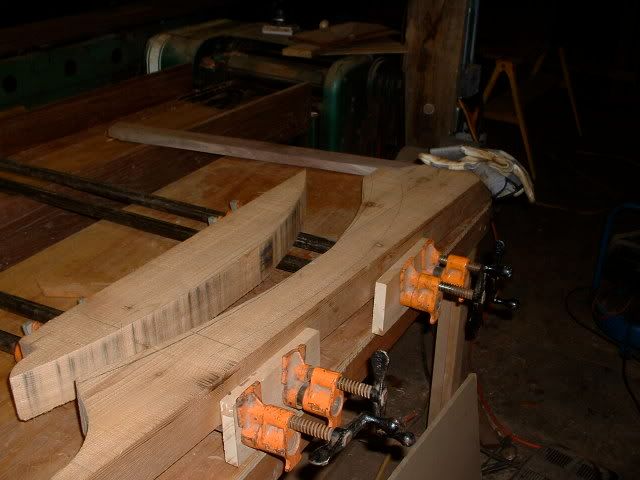
i make a backing strap from a 1 1/4" bandsaw blade-i cut two 36" lengths grind off the teeth and use duct (duck) tape to hold the two together-
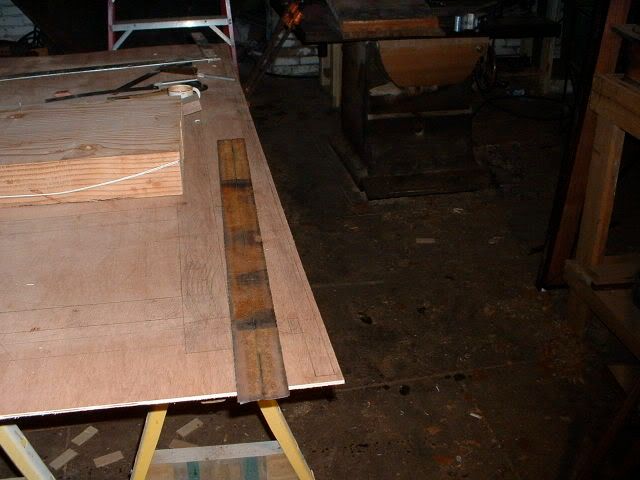
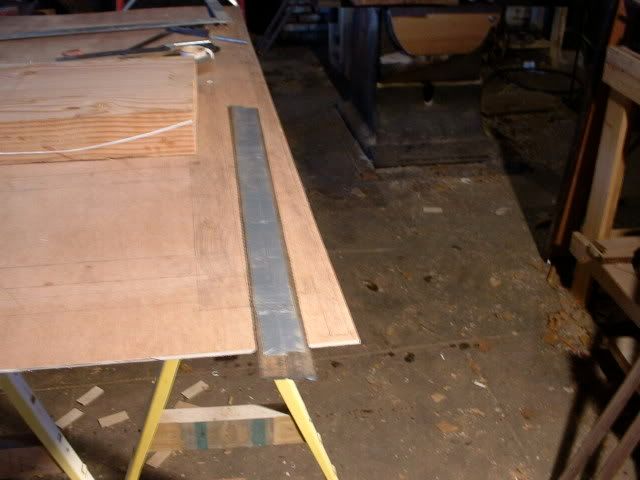
also i cut two pieces of 1/16" plastic to put on each side of the piece of walnut i'll be bending-this is so i want get weird colors from the metal strap and from the fir-
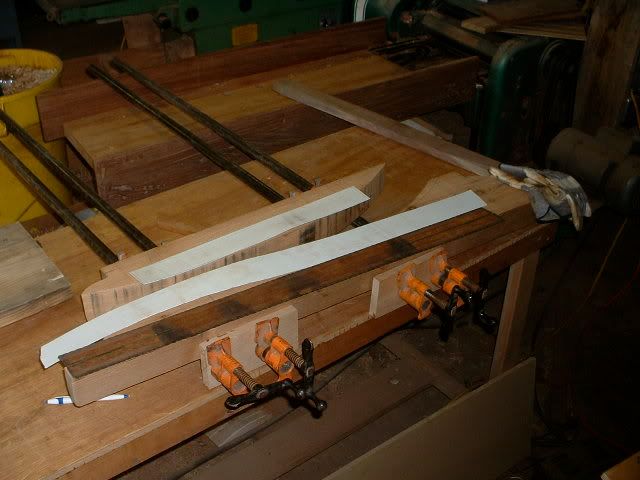
i make a simple drying jig-
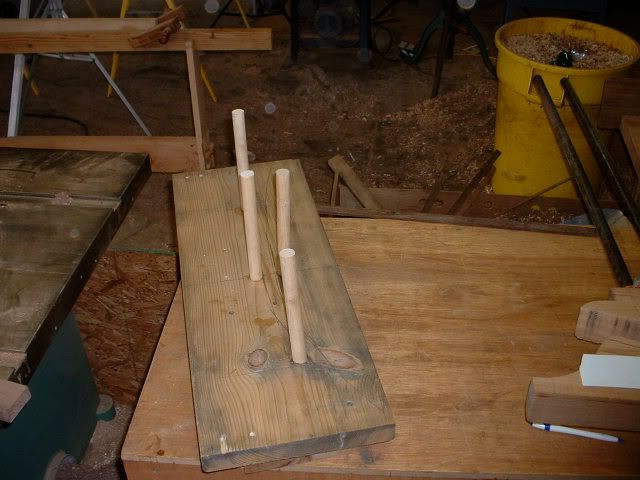
then it's for real-#1- i need nine-
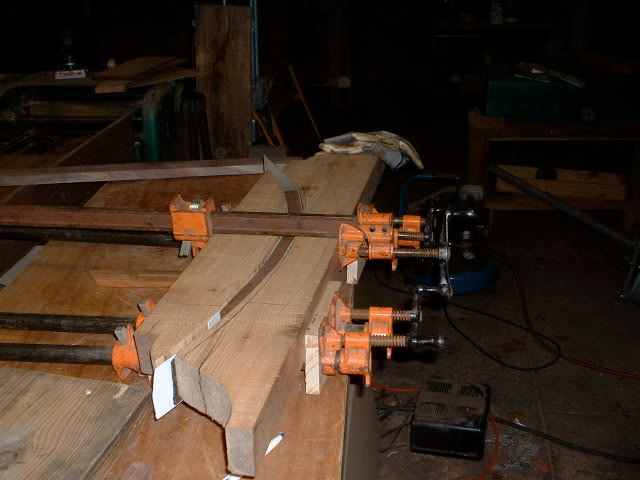
i steam three at a time one hour plus-then in the mold for 15 min. then in the drying jig for 24 hours-
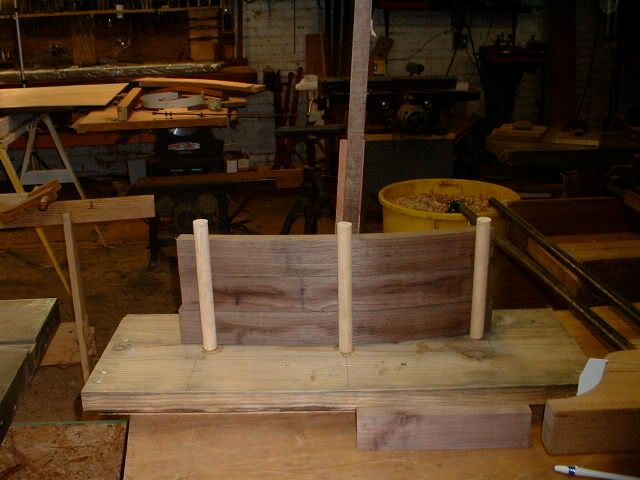
the real thing-
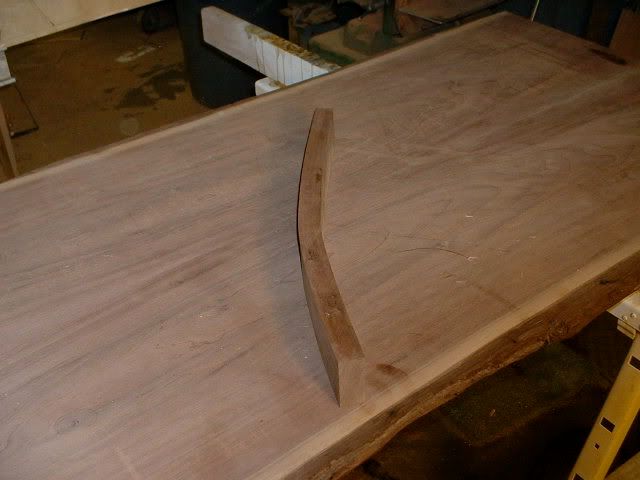
it all revolves around this curve-now that i have it for real i can make a true templet for the legs and a mold for the curved veneer panels-
templet-
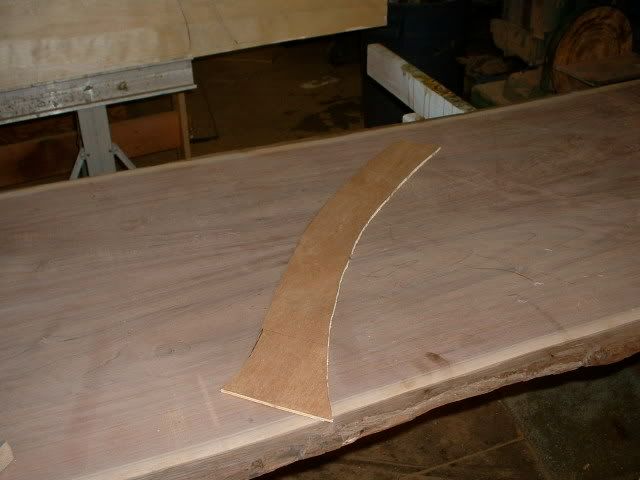
to make the mold for the panels i use a piece of fir-
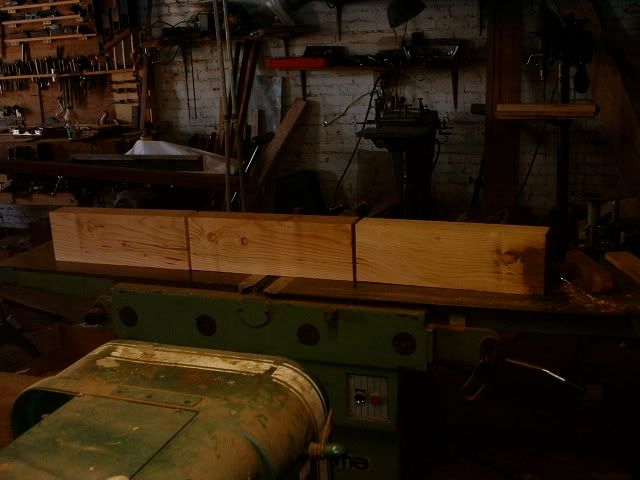
i join two of these pieces and band saw the curve- then i line it with 1/16" plastic-
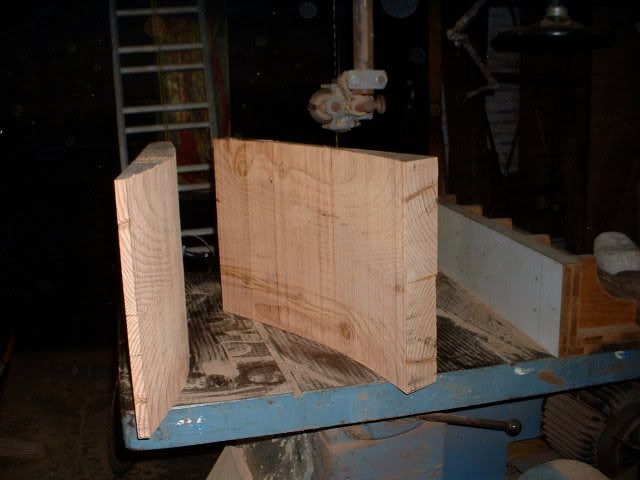
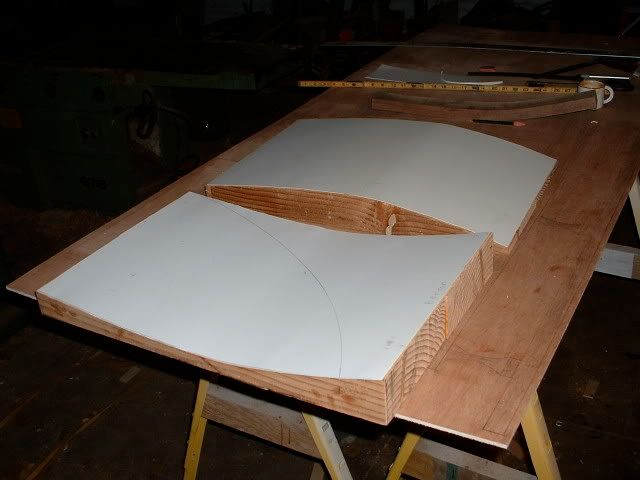

more to come-
alex