- Messages
- 12,167
- Location
- Constantine, MI
This is related to the grandfather clock I'll be building this fall for a customer in CA. I found a coppersmith in Ohio that is doing the clock face for that clock and, as is his custom, when doing something he has not done before he will make a scaled down version to test technique and process. The face of this clock was actually his practice piece for the big clock. My CA client was so impressed (as was I) with the test face that he commissioned me to build a 'simple' frame for it. As all the other pieces I am building for this customer are in the Greene & Green style and in walnut, this seemed to be simple, but keeping with the theme. The sapwood was intentional and at the customer's request.
Shown here with one application of natural Danish oil, it will get several applications of a satin varnish before it ships - it will hang in a kitchen and will need the extra protection.
If you ever need copper work on any kind I would highly recommend John Monk at luminesque.com. He is an artist of the highest caliber and an absolute gentleman to deal with. The final picture is of the large clock face and the hinges he made for my grandfather clock project.
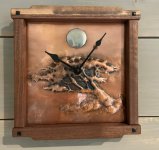
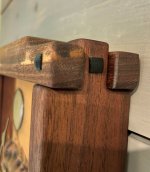
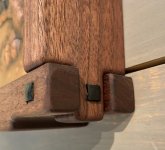
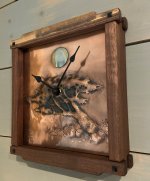
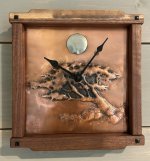
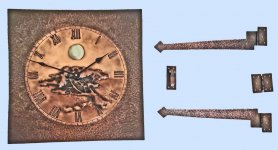
Shown here with one application of natural Danish oil, it will get several applications of a satin varnish before it ships - it will hang in a kitchen and will need the extra protection.
If you ever need copper work on any kind I would highly recommend John Monk at luminesque.com. He is an artist of the highest caliber and an absolute gentleman to deal with. The final picture is of the large clock face and the hinges he made for my grandfather clock project.
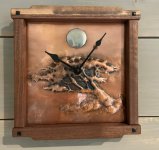
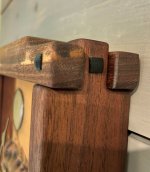
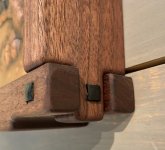
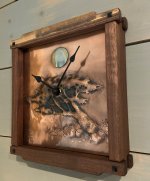
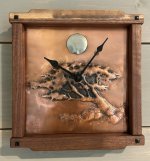
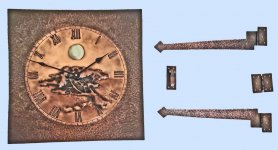