glenn bradley
Member
- Messages
- 11,641
- Location
- SoCal
After we had out-of-town guests a while back it became painfully obvious that we needed some sort of night stands in one of the guest rooms. With the holidays coming LOML moved this up on the list. She showed me a style that is not my usual thing. After some discussion we arrived at a design that she liked. I'll show that later. For now I will just go through the motions. 
I wanted to use up some more of this sappy or odd-man-out material.
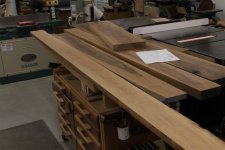
There will be square tapered legs. I'm sure many folks use this trick to select the orientation of the figure to get a good look on as many faces of the leg as possible.
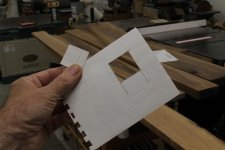
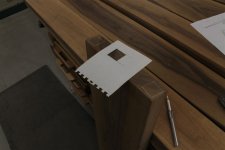
Here's a random thing I do that may help someone or give them an even better idea. This is a magnet wrapped in some tape to get the amount of pull I am happy with.
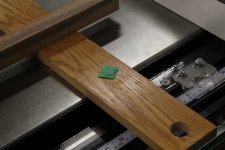
I stick it to a 1-2-3 block.
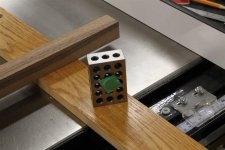
I stick the block to the table saw top. I set the fence 3" more than the measurement I am after to make a quick, safe, length-stop.
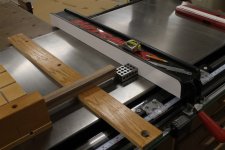
The board laying there is just a support. It is made from a finish test-board for a jewelry cabinet I made LOML 18 years ago
. It happened to be the same thickness as my sled bases so way back when I recessed a couple of magnets in it.
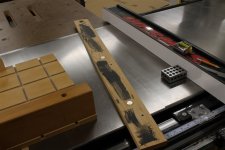
The magnets along with some brush-on rubber product make the board stay put. I generally only use it on longer stock but it was handy and seemed to help out. At any rate, the milled leg blanks are cut to length.
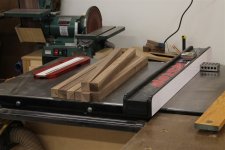
I pull the taper jig down off the wall and taper the two "inside" faces of the legs.
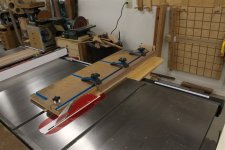
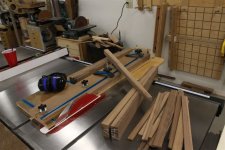
I also rough mill some blanks for the aprons and the tops.
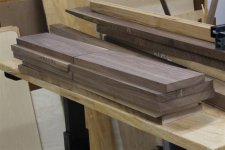
I will sticker these for a couple of days while I fool around with the drawer parts.
I wanted to use up some more of this sappy or odd-man-out material.
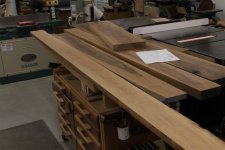
There will be square tapered legs. I'm sure many folks use this trick to select the orientation of the figure to get a good look on as many faces of the leg as possible.
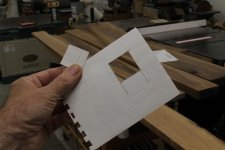
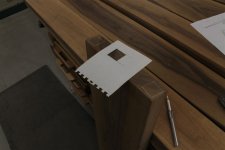
Here's a random thing I do that may help someone or give them an even better idea. This is a magnet wrapped in some tape to get the amount of pull I am happy with.
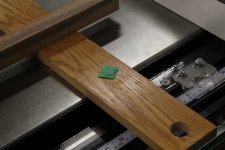
I stick it to a 1-2-3 block.
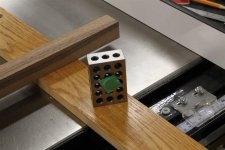
I stick the block to the table saw top. I set the fence 3" more than the measurement I am after to make a quick, safe, length-stop.
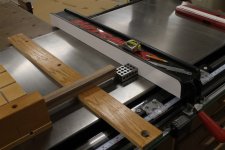
The board laying there is just a support. It is made from a finish test-board for a jewelry cabinet I made LOML 18 years ago
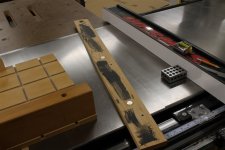
The magnets along with some brush-on rubber product make the board stay put. I generally only use it on longer stock but it was handy and seemed to help out. At any rate, the milled leg blanks are cut to length.
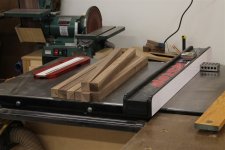
I pull the taper jig down off the wall and taper the two "inside" faces of the legs.
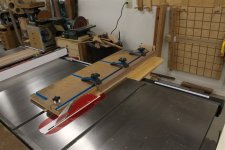
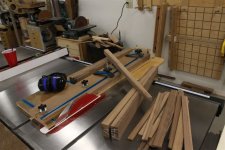
I also rough mill some blanks for the aprons and the tops.
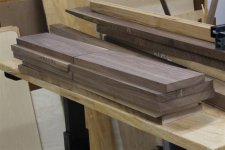
I will sticker these for a couple of days while I fool around with the drawer parts.