- Messages
- 12,168
- Location
- Constantine, MI
Most of you who have either visited my shop or seen pictures know that it is not really large and I like to keep it neat and somewhat organized. Well, one of those things has not changed, but the other two have taken a turn for the worse. As I put more and more projects behind me I am accumulating more and more lumber, jigs, templates and tools. What I am not getting is more space to keep them in.
So, I am undertaking a few projects to, at least, partially remedy the problem. The first thing to tackle is to find more places to put things. I have always been aware that I have a lot of under utilized spaces under tools and over the work bench. The most obvious seemed to be under the drill press and under the drum sander. There's loads of available drawer and cubby space to be had there for little investment. Also, there are lots of ideas on the net for making good use of that space. So, those two are definitely on the schedule. There are also similar opportunities beneath the planer and under the TS extension table. The planer (DW735) has a remote chance of being upgraded someday so I think I'll hold on that. The TS extension has oodles of space but I have a right tilt saw (so the base access is on the right side and opens under the extension) and I also have the TS on a roller base with a member that cuts through that space. Any storage solution for that space will have to take those things into consideration.
Needing to be encouraged with a quick win I decided to go with the over bench storage first. Mostly because I already have the casters, a sheet of 3/4 birch, and enough red oak for the doors and face frame in the shop. So, $35 worth of 2x4 is all I needed to buy. The bench sits in front of the overhead door so everything must be free standing.
Solution #1 - Over the bench storage
Having something hanging over the bench is not optimal. It can get in the way or make you feel claustrophobic. My bench, unlike the one pictured here, has a tool trough that runs the entire width of the bench so the actual work surface is only at the front of the bench. I also decided to use a cantilever design with casters. Now, if there is an "airspace" conflict it can be easily and temporarily solved. The last consideration was that it could not be taller than the bottom of the windows in the door. They provide the only natural light that gets into the shop.
Here's what I came up with. For the moment it provides storage for the Domino, hanging space for small oft-used tools, and some cabinet space. I'm thinking of maybe adding a plane till. As always, comments are welcome.
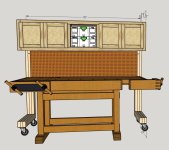
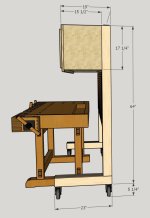
So, I am undertaking a few projects to, at least, partially remedy the problem. The first thing to tackle is to find more places to put things. I have always been aware that I have a lot of under utilized spaces under tools and over the work bench. The most obvious seemed to be under the drill press and under the drum sander. There's loads of available drawer and cubby space to be had there for little investment. Also, there are lots of ideas on the net for making good use of that space. So, those two are definitely on the schedule. There are also similar opportunities beneath the planer and under the TS extension table. The planer (DW735) has a remote chance of being upgraded someday so I think I'll hold on that. The TS extension has oodles of space but I have a right tilt saw (so the base access is on the right side and opens under the extension) and I also have the TS on a roller base with a member that cuts through that space. Any storage solution for that space will have to take those things into consideration.
Needing to be encouraged with a quick win I decided to go with the over bench storage first. Mostly because I already have the casters, a sheet of 3/4 birch, and enough red oak for the doors and face frame in the shop. So, $35 worth of 2x4 is all I needed to buy. The bench sits in front of the overhead door so everything must be free standing.
Solution #1 - Over the bench storage
Having something hanging over the bench is not optimal. It can get in the way or make you feel claustrophobic. My bench, unlike the one pictured here, has a tool trough that runs the entire width of the bench so the actual work surface is only at the front of the bench. I also decided to use a cantilever design with casters. Now, if there is an "airspace" conflict it can be easily and temporarily solved. The last consideration was that it could not be taller than the bottom of the windows in the door. They provide the only natural light that gets into the shop.
Here's what I came up with. For the moment it provides storage for the Domino, hanging space for small oft-used tools, and some cabinet space. I'm thinking of maybe adding a plane till. As always, comments are welcome.
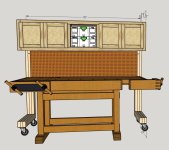
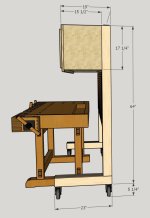