- Messages
- 8,673
- Location
- Thomasville, GA
First of all, I want to thank Brent and Darren for their input on various aspects of my struggles with gcode senders on RPi. Their help and some perseverance on my part got me where I wanted to be.
A short walk through my history with this: Setting up an RPi3 was no issue in itself. My biggest problem was getting a sender running on RPi for evaluation.
UGS installed and ran just fine, but its graphics (Visualizer) won't work on RPi.
CNCjs had plenty of instructions but I never got it running until I found a CNCjs/RPi OS bundle. When I installed that, it worked great. It requires a browser on a PC to run it, but I wanted a headless system, if possible.
I tried bCNC via the detailed step-by-step commands for installation on RPi, but every time I made a step forward, there was another step back. Further research found instructions for the process of downloading a zip file for bCNC, loading it onto RPi and extracting it in place. I'm pleased to say it worked just fine - no problem.
Accessing the RPi remotely from a PC was no problem using the VNC application built into RPi.
File sharing was the next matter to deal with and that was accomplished with Samba. It required a number of configuration tweaks, but it works as it should. I map a drive letter via Windows File Manager and copy files both directions.
After getting everything working to satisfaction, I realized I hadn't detailed my steps well, so I went back through them and documented them.
When I was satisfied with the entire package, I read the SD card into an image file so I could replicate it onto other SD cards. I had built the system on an RPi3 I labeled 'RPi-LSR'. After writing the image onto another SD card for my CNC, all I had to do was change the device name and I was done.
Here's a view of bCNC via VNC Viewer:
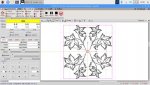
This process allows bCNC to run headless, so losing the connection between the PC and RPi won't kill a run.
Fun stuff!
A short walk through my history with this: Setting up an RPi3 was no issue in itself. My biggest problem was getting a sender running on RPi for evaluation.
UGS installed and ran just fine, but its graphics (Visualizer) won't work on RPi.
CNCjs had plenty of instructions but I never got it running until I found a CNCjs/RPi OS bundle. When I installed that, it worked great. It requires a browser on a PC to run it, but I wanted a headless system, if possible.
I tried bCNC via the detailed step-by-step commands for installation on RPi, but every time I made a step forward, there was another step back. Further research found instructions for the process of downloading a zip file for bCNC, loading it onto RPi and extracting it in place. I'm pleased to say it worked just fine - no problem.
Accessing the RPi remotely from a PC was no problem using the VNC application built into RPi.
File sharing was the next matter to deal with and that was accomplished with Samba. It required a number of configuration tweaks, but it works as it should. I map a drive letter via Windows File Manager and copy files both directions.
After getting everything working to satisfaction, I realized I hadn't detailed my steps well, so I went back through them and documented them.
When I was satisfied with the entire package, I read the SD card into an image file so I could replicate it onto other SD cards. I had built the system on an RPi3 I labeled 'RPi-LSR'. After writing the image onto another SD card for my CNC, all I had to do was change the device name and I was done.
Here's a view of bCNC via VNC Viewer:
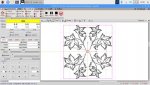
This process allows bCNC to run headless, so losing the connection between the PC and RPi won't kill a run.
Fun stuff!
Last edited: