Stuart Ablett
Member
- Messages
- 15,917
- Location
- Tokyo Japan
I'm in the process of bidding another chair-like prop for my favorite Canadian Circus (please don't say their name, just trying to keep a low profile).
This will be a chair or two (I'm trying to get them to buy two for a good price, as we all know with chairs making two is NOT double the price as you already have all the jigs and such built) that is used in a highwire act......
Twice daily the chair gets dropped from a height onto the wirenet then when the act is over the wirenet gets released the the chair hits the stage from about 6 feet up, it comes down a different way each time and over time the chair gets busted up.
The chair is reinforced in key areas with steel, which I'll have to make as well, and the weight is to be between 6-7Kg 13-15lbs about. I've already identified some things that can be improved upon the existing design, that will make it a lot stronger and will not add any weight.
OK what I'm putting out there for everyone is what kind of glue should I use?
A typical PVA white glue would work, I'm sure, but what about something that is good and solid but has some flex to it?
A gorilla glue or an epoxy?
I'm open to all ideas here, this is a high end build that has to be better than good, and it has to be durable too.
The wood used will be Beech, I think it is a good choice for strength and durability, it is often used in chair construction and is not bad to work with. It is expensive here in Tokyo, but hey, so is everything else. I'm planning on using typical mortise and tenon joints and I think I'll pin these joints to make them extra strong. I have a time frame that the chairs would have to ship before the middle of June, so I do have some time, but as you know I'm really busy with other stuff too, so I need to get in front of this, so I'm looking for ideas.
I cannot share the plans with you for obvious reasons, but it is a basic chair, the base is a bit wider side to side and back to front than the seat, but not much, the legs have about a 3 degree splay. The chair back is straight up and down, not like a real chair, it is a prop.
Your thoughts on all of this would be appreciated, I have a pretty good idea about how I'm going to prototype it and then build it, but I would be a fool if I did not ask for more input.
Thanks!
This will be a chair or two (I'm trying to get them to buy two for a good price, as we all know with chairs making two is NOT double the price as you already have all the jigs and such built) that is used in a highwire act......
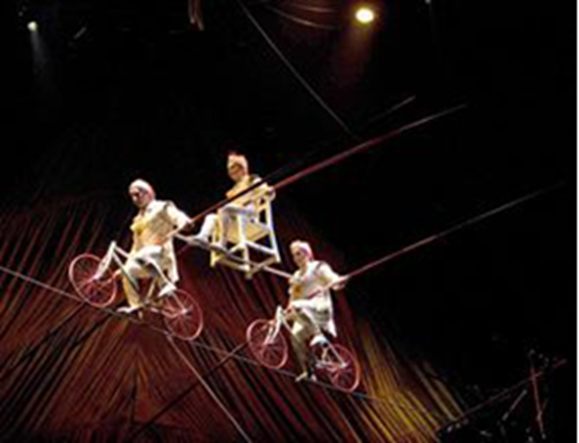
Twice daily the chair gets dropped from a height onto the wirenet then when the act is over the wirenet gets released the the chair hits the stage from about 6 feet up, it comes down a different way each time and over time the chair gets busted up.
The chair is reinforced in key areas with steel, which I'll have to make as well, and the weight is to be between 6-7Kg 13-15lbs about. I've already identified some things that can be improved upon the existing design, that will make it a lot stronger and will not add any weight.
OK what I'm putting out there for everyone is what kind of glue should I use?
A typical PVA white glue would work, I'm sure, but what about something that is good and solid but has some flex to it?
A gorilla glue or an epoxy?
I'm open to all ideas here, this is a high end build that has to be better than good, and it has to be durable too.
The wood used will be Beech, I think it is a good choice for strength and durability, it is often used in chair construction and is not bad to work with. It is expensive here in Tokyo, but hey, so is everything else. I'm planning on using typical mortise and tenon joints and I think I'll pin these joints to make them extra strong. I have a time frame that the chairs would have to ship before the middle of June, so I do have some time, but as you know I'm really busy with other stuff too, so I need to get in front of this, so I'm looking for ideas.
I cannot share the plans with you for obvious reasons, but it is a basic chair, the base is a bit wider side to side and back to front than the seat, but not much, the legs have about a 3 degree splay. The chair back is straight up and down, not like a real chair, it is a prop.
Your thoughts on all of this would be appreciated, I have a pretty good idea about how I'm going to prototype it and then build it, but I would be a fool if I did not ask for more input.
Thanks!