Tom Baugues
Member
- Messages
- 2,905
- Location
- Lafayette, Indiana
Now that I have sharper tools I threw another piece of Mulberry on the lathe tonight and it was turning so well with shavings flying 6-8 feet across the room. I was really enjoying the process when I stopped to check my progress and noticed this long crack across the bottom. It looks to me to be a fatal crack and I'm afraid that the bowl might fly apart in halves if I continue. I have no desire to catch a 10 lb. chuck of flying wood with my face. So what do you think? Looking at the photos....would you continue to turn this?
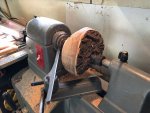
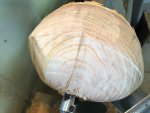
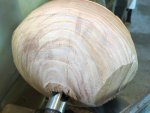
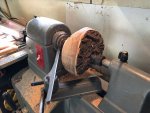
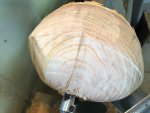
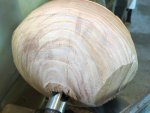