I don’t know if any of you is aware of the 5S method. It has been applied in many companies, with different results depending on the company and the comitment to it. However, it can also be applied to particular households if one wants to. But it takes effort and comitmment. And if you ask if I have applied it to my shop, my answer is NO, but I want to, and I am selfconvincing myself that I have to. So here I post it for those who might want to clear up some room in their shops and get rid of stuff.
The 5S quality tool is derived from five Japanese terms beginning with the letter "S" used to create a workplace suited for visual control and lean production. The pillars of 5S are simple to learn and important to implement:
- Seiri: To separate needed tools, parts, and instructions from unneeded materials and to remove the unneeded ones.
- Seiton: To neatly arrange and identify parts and tools for ease of use.
- Seiso: To conduct a cleanup campaign.
- Seiketsu: To conduct seiri, seiton, and seiso daily to maintain a workplace in perfect condition.
- ****suke: To form the habit of always following the first four S’s.
Below, the Japanese terms are translated into the English language version of the 5S’s.
Japanese | Translated | English | Definition |
Seiri | organize | sort | Eliminate whatever is not needed by separating needed tools, parts, and instructions from unneeded materials. |
Seiton | orderliness | set in order | Organize whatever remains by neatly arranging and identifying parts and tools for ease of use. |
Seiso | cleanliness | shine | Clean the work area by conducting a cleanup campaign. |
Seiketsu | standardize | standardize | Schedule regular cleaning and maintenance by conducting seiri, seiton, and seiso daily. |
****suke | discipline | sustain | Make 5S a way of life by forming the habit of always following the first four S’s. |
Obviously these do not apply to Glenn, who is an example to follow In many aspects.
Toni,
YES - YES - YES
I think it is very difficult to really grasp the 5S plan if you have never been trained in HOW to do it. It is really a lot of work and a lot of premeditated planning.
I have been involved in several Kaizan events and been through several training sessions.
That was done on an industrial scale.
We went as far as to video the entire event, so we could watch it and see how we could have done better, for next time.
Japan does these things at Toyota, which is seriously larger than the manufacturing plants I have worked in.
I am pretty sure VW and Bosch (Bosch is an ENORMOUS factory) also do it.
You can do it piece by piece, but the best way is the entire shop all at one time. Again, with a premediteted plan.
I think lots of us have at one time or another done scale paper cutouts of shop machines on the floor space or done it in CAD.
That's all good but that is only a piece of 5S
5S is about all the "STUFF", clutter, junk.
Another big point in organizing the shop is POU Point Of Use
If you need a 30mm or 21mm open end wrench - cut off the box end - make it short so that you do not over tighten the collet - and put the wrench right where you NEED it to be.
This is the TOP drawer in a cabinet I make for my CNC machine.
EASY access - ONLY what I need is in that drawer. This is my third iteration of this drawer.
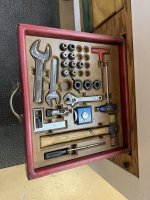
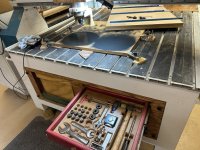
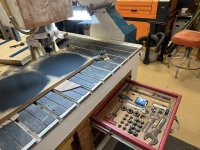
You can see the spindle RIGHT there, where I change the tools.
I am kinda happy with it, but it could be improved.
I have 5s'd my entire shop twice.
I need to do it again maybe 2 more times.
I do not store any wood in my shop.